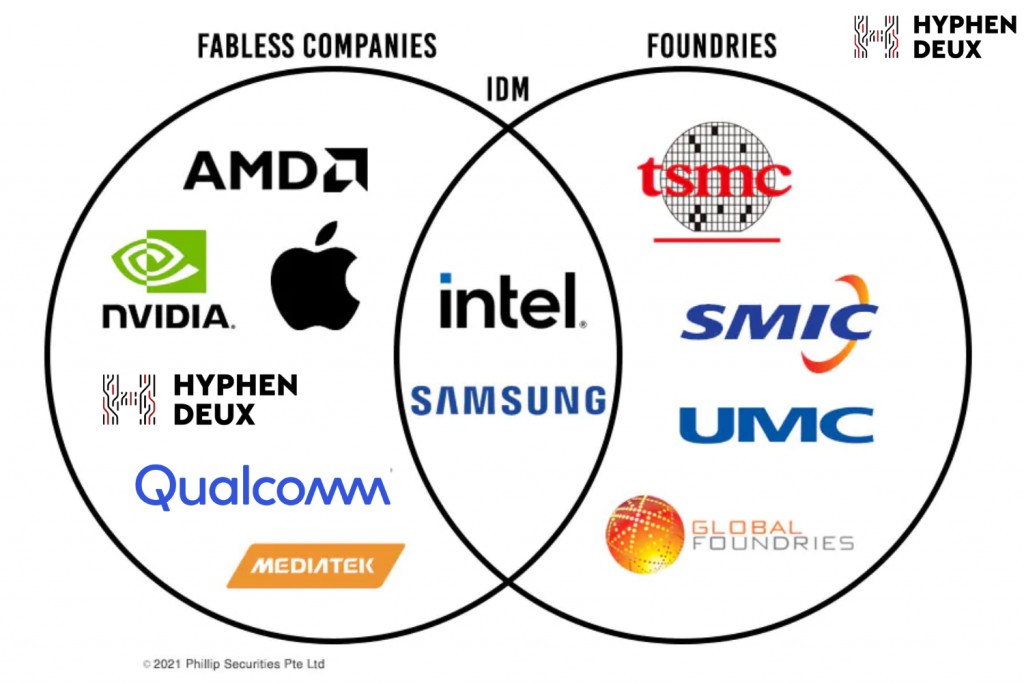
Fabless Design – 04 Business Models Transforming in Semiconductor Field
Contents
Fabless Design: Driving Innovation in the Semiconductor Industry
In today’s technologically advanced world, the intricate devices we rely on, from smartphones to autonomous vehicles, security cameras, home appliances are powered by tiny marvels known as semiconductors. The semiconductor industry is a dynamic and critical sector, powering the devices that have become integral to our daily lives. Within this industry, companies employ different business models to navigate the complex landscape of semiconductor design and manufacturing. In this blog post, we will explore 04 business models in the Semiconductor Design & Manufacturing ecosystem: IDM (Integrated Device Manufacturer), Fabless design, Foundry, and Fab-lite.
-
Integrated Device Manufacturers (IDM)
The IDM model represents a holistic approach to semiconductor manufacturing. In this model, a single company controls all phases of production, from research and development (R&D) to chip fabrication and packaging. This vertical integration allows for streamlined communication between teams, resulting in greater efficiency and faster time-to-market.
Examples: Intel, Samsung, Texas Instruments.
Pros:
- Control Over Entire Process: IDMs oversee every aspect of chip development, from conception to production.
- Innovation: Tight integration of design and manufacturing teams facilitates rapid innovation.
- Customization: Ability to produce custom chips for specific applications.
Cons:
- High Capital Expenditure: Building and maintaining semiconductor fabrication facilities requires substantial capital investment.
- Resource Intensiveness: Managing both design and manufacturing operations can be resource-intensive.
- Market Volatility: IDMs may face challenges adapting to market changes due to extensive in-house manufacturing commitments.
-
Fabless Design
Fabless companies innovate, design, and market microchips while outsourcing wafer processing, packaging, and testing to third-party partners. They partner with foundries such as TSMC and GlobalFoundries to print designs on wafers and contract out testing and packaging services to outsourced semiconductor assembly and testing (OSAT) providers. Clients of design companies are original equipment manufacturers (OEMs) or end-user device innovators incorporating microchips into their products.
Examples: Qualcomm, Nvidia, Broadcom, MediaTek, AMD, Hyphen Deux (a Vietnamese start-up specializing in microcontrollers for IoT, automotive, industrial, and AI chips).
Pros:
- Lower Upfront Costs: Outsourcing manufacturing allows these companies to focus on design innovation.
- Flexibility: Ability to choose the best foundry for each chip based on features or cost.
Cons:
- Reliance on Foundries: Dependent on foundries for production capacity and pricing.
- Less Control: Reduced control over manufacturing quality and timelines compared to IDMs.
-
Pure-play Foundry
A semiconductor foundry, also known as a fab, is a factory where silicon wafers are manufactured. The main customers of a semiconductor foundry are chip makers such as Hyphen Deux, Qualcomm, Intel, AMD… Foundries emerged in response to the growing need for semiconductor devices, driving the electronics industry towards larger and more efficient fabrication plants.
Examples: Taiwan Semiconductor Manufacturing Company (TSMC), GlobalFoundries, SIMC.
Pros:
- Cost-Efficiency: Fabless companies can avoid high upfront costs associated with building and maintaining fabs.
- Global Presence: Foundries often serve a global clientele, contributing to a diverse customer base.
- Scalability: Easy scalability to accommodate the needs of various clients.
Cons:
- Dependency: Foundries rely on fabless companies for design, tying their success to their clients’ success.
- Limited Control: Lack of control over the entire process may lead to optimization challenges.
- Intense Competition: The foundry market is highly competitive, with several major players vying for business.
-
Fab-lite Model
The Fab-lite model is a hybrid approach where a company owns some semiconductor fabrication facilities but also outsources some production to external foundries. This model offers a balance between in-house production and outsourcing.
Example: GlobalFoundries.
Pros:
- Flexibility: Leverage in-house facilities for critical processes while outsourcing non-core production.
- Risk Mitigation: Reduces dependence on a single manufacturing model.
- Cost Control: Optimize costs by balancing internal and external manufacturing resources.
Cons:
- Complex Management: Managing both in-house and outsourced production can be operationally complex.
- Integration Challenges: Combining internally and externally manufactured components may pose technical challenges.
- Dependency on External Partners: Reliance on external foundries introduces potential supply chain risks.
Conclusion
The semiconductor industry’s evolution is driven by the interplay between IDM, fabless, foundry, and fab-lite models. As technology advances, these business models will adapt to meet the ever-changing demands of the market. Collaboration, specialization, and adaptability will be key factors in navigating the intricate landscape of semiconductor manufacturing, ultimately shaping the technological innovations that define our future.
(Source: techovedas)